Ship welding is a critical aspect of the Philippine maritime industry, playing a pivotal role in constructing and maintaining vessels that traverse the vast seas. In the Philippines, known for its rich maritime heritage and skilled workforce, ship welding and metal fabrication have become an integral part of the country’s booming shipbuilding industry. With its strategic location in Southeast Asia and abundant supply of raw materials, the Philippines has earned a reputation for delivering high-quality ships to global markets. This ultimate guide will delve into the world of ship welding and metal fabrication in the Philippines, exploring its importance, techniques used, and training opportunities available and highlighting some remarkable projects that showcase the nation’s expertise on a global scale.
Click here to view our ship welding and metal fabrication capabilities.
Overview of Ship Welding and Metal Fabrication in the Philippines
The Philippines has emerged as a key player in ship welding and metal fabrication thanks to its skilled Filipino workforce and strategic location. The country’s strong maritime tradition has led to the development of a robust industry that caters not only to domestic needs but also exports products across the globe. Ship welding and metal fabrication companies in the Philippines pride themselves on their ability to meet international quality standards, ensuring that their clients receive top-notch products.
One of the factors that set ship welding and metal fabrication in the Philippines apart is the level of expertise possessed by local welders. Many of them have undergone specialized training programs to hone their skills, making them highly sought after in both local and international markets. In addition, Filipino welders are known for their attention to detail, precision, and dedication to producing work of exceptional quality.
Moreover, the geographical location of the Philippines enhances its position as an ideal hub for ship welding and metal fabrication. Its archipelagic nature allows for easy access to various ports around Southeast Asia, enabling businesses in the industry to efficiently transport raw materials and finished products. This geographic advantage plays a significant role in reducing transportation costs while ensuring prompt delivery times.
Ship welding and metal fabrication play a vital role in supporting both Philippine and international maritime industries. With its skilled workforce and strategic location, the Philippines has positioned itself as a leading player in this sector.

History: Evolution of Ship Welding in the Philippines
Ship welding in the Philippines has a long and storied history, with its origins dating back centuries. The Spanish colonization of the Philippines in the 16th century brought with it advancements in shipbuilding techniques, including the use of metal welding. Initially, ship welders used simple methods such as forge welding, where two pieces of metal were heated and hammered together to create a strong bond. Over time, however, more sophisticated welding techniques emerged as technology improved.
The introduction of electric arc welding in the late 19th century revolutionized shipbuilding in the Philippines. This new method allowed for faster and more efficient joining of metal parts, resulting in stronger and more durable ships. Shipyards across the country quickly adopted this technology, enabling them to meet growing demands for maritime transportation. Today, modern shipyards in the Philippines utilize advanced automated processes like robotic welding systems to enhance production efficiency and precision.
With a rich heritage rooted in both tradition and innovation, ship welding continues to play a crucial role in shaping the maritime industry in the Philippines. The evolution of shipbuilding techniques from basic forge welding to state-of-the-art automated systems is a testament to Filipino craftsmanship and adaptability. As technology advances further, it’s exciting to think about what new possibilities lie ahead for shipbuilders as they continue their vital work on forging strong connections between land and sea through exceptional welds.
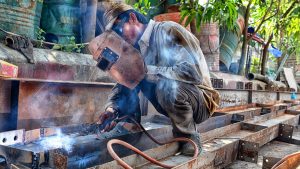
Importance of Ship Welding: Ensuring Structural Integrity of Filipino Vessels
Ship welding plays a crucial role in ensuring the structural integrity of vessels in the Philippines. Without proper and sturdy welds, a ship would be at risk of structural failure, which could lead to catastrophic consequences. The continuous welding joints throughout the ship’s structure provide much-needed strength and stability.
One of the main reasons why ship welding is so important is because ships are constantly subjected to various forces, such as waves, wind, and heavy loads, that can cause significant stress on their structures. Welding helps distribute these forces evenly across the entire vessel, reinforcing its ability to withstand external pressure. It is essential for welders to use high-quality materials and follow strict guidelines to ensure that each weld joint can endure these demanding conditions.
Moreover, ship welding also contributes to the safety of those onboard by reducing risks associated with leakage or structural failure. With proper welding techniques, potential weak points or gaps in the structure can be eliminated, preventing water from entering critical areas like ballast tanks or fuel storage compartments. By maintaining watertight seals through effective welding practices, ships are safeguarded against accidents and environmental damage caused by leakage.
Ship welding in the Philippines cannot be underestimated when it comes to ensuring the structural integrity of vessels. It provides the strength and stability necessary for withstanding external forces while promoting a safe environment for all onboard.
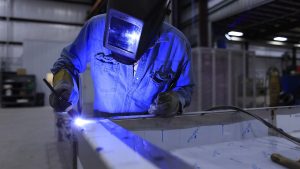
The Role of Metal Fabrication in Shipbuilding in the Philippines
In the vibrant shipbuilding industry of the Philippines, metal fabrication plays a crucial role in ensuring the structural integrity and functionality of vessels. From large cargo ships to luxury yachts, every aspect of ship construction heavily relies on skilled metal fabricators who meticulously shape and join various metal components together. The process involves cutting, bending, welding, and assembling steel plates and pipes to create the intricate framework that supports the entire vessel.
What sets metal fabrication in shipbuilding apart is not just its technical complexity but also its adherence to strict international standards. Shipbuilders in the Philippines must comply with regulations set by maritime classification societies to ensure their vessels meet stringent safety requirements. Metal fabricators take on this challenge by using specialized equipment and techniques that enable them to achieve precise measurements and welds required for structural strength at sea.
Moreover, effective utilization of high-quality materials is vital for constructing durable ships. Metal fabricators are responsible for selecting appropriate steel grades that exhibit excellent corrosion resistance properties while also considering factors such as weight reduction for fuel efficiency. By leveraging their extensive knowledge and expertise, these professionals ensure that each component used in ship construction meets both functional requirements and industry standards.
It is clear that metal fabrication plays an indispensable role in shipbuilding in the Philippines. Without skilled fabricators proficient in cutting-edge techniques and dedicated to adhering to international regulations, constructing seaworthy vessels would be nearly impossible.
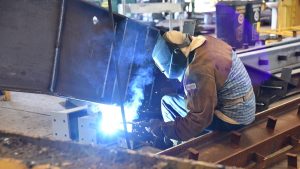
Metal Fabrication in the Philippines: Industry Growth and Opportunities
The metal fabrication industry in the Philippines has experienced significant growth in recent years, driven by both domestic demand and international exports. With the country’s strategic location and skilled workforce, it has become a preferred destination for companies looking to outsource their metal fabrication needs. The sector is expected to continue expanding as more industries recognize the benefits of outsourcing their metal fabrication requirements to Filipino manufacturers.
This rapid growth offers vast opportunities for individuals interested in pursuing a career in metal fabrication. As companies expand their operations, they will require skilled workers who possess expertise in areas such as welding, machining, and sheet metal fabrication. By acquiring these skills and staying updated with current industry trends and technologies, individuals can carve out lucrative careers within the sector. Additionally, there is potential for entrepreneurs to establish their own metal fabrication businesses to cater to both local and international clients.
The boom in the Philippine metal fabrication industry also presents various economic benefits for the country. Increased manufacturing activities fuel job creation and stimulate economic growth while attracting foreign investments that contribute to technology transfer and knowledge sharing. Moreover, promoting local suppliers of raw materials further enhances its overall impact on the economy by boosting ancillary industries related to metals, such as mining, metallurgy research & development facilities, among others.
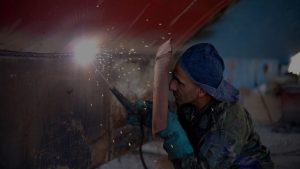
Types of Ship Welding Techniques: MIG, TIG, Arc Welding
Metal fabrication and welding are vital components of ship repair and shipbuilding in the Philippines, ensuring the structural integrity of vessels that navigate treacherous waters. Among the various ship welding techniques available, MIG, TIG, and Arc welding stand out as the most commonly used methods.
MIG (Metal Inert Gas) welding is renowned for its versatility and ability to join metals together quickly. With a continuous wire feed electrode and shielding gas to protect the weld area from contamination, MIG welding offers high deposition rates and can be automated for efficiency. This technique is ideal for thick metal sections commonly found in shipbuilding.
On the other hand, TIG (Tungsten Inert Gas) welding excels in creating precise and aesthetically appealing welds. Using a non-consumable tungsten electrode with an inert shielding gas like argon or helium, this technique allows for better control over heat input and weld pool size. TIG welding is often preferred when working with thin sheets or in situations where exceptionally clean welds are required.
Lastly, arc welding encompasses several subcategories, such as SMAW (Shielded Metal Arc Welding), FCAW (Flux-Cored Arc Welding), and SAW (Submerged Arc Welding). These techniques utilize an electric arc between an electrode and a workpiece to generate the heat necessary for fusion. They are commonly used in heavy-duty applications like shipbuilding due to their ability to penetrate thick materials deeply. However, their use can lead to excessive heat build-up if not managed properly.
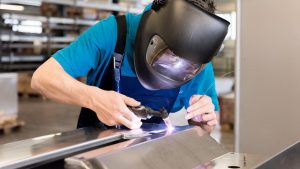
Key Considerations in Ship Welding: Safety Regulations and Materials
Ship welding is a critical process in shipbuilding and maintenance, but it also carries significant safety risks if not performed properly. That’s why strict safety regulations are in place to protect workers and ensure the integrity of the ship’s structure. Shipyards must adhere to guidelines set by regulatory bodies such as the Occupational Safety and Health Administration (OSHA) and the International Maritime Organization (IMO). These regulations cover areas such as hazard communication, personal protective equipment (PPE), ventilation systems, fire prevention measures, and safe work practices. Adhering to these safety regulations is essential to prevent accidents, injuries, or even catastrophic incidents.
When it comes to ship welding projects, choosing the right materials is crucial for ensuring the long-term durability of the vessel. Various factors come into play when selecting appropriate materials for ship construction or repair jobs. Factors such as corrosion resistance, strength-to-weight ratio, weldability, and cost efficiency should all be carefully considered. Depending on specific requirements and environmental conditions that ships may encounter – including saltwater exposure or extreme temperatures – different stainless steels or alloys might be more suitable than conventional carbon steel options. Additionally, using high-quality filler metals can improve weld quality while minimizing defects like porosity or cracking.
Prioritizing safety regulations during ship welding projects is paramount to minimize risks during construction or maintenance work. Adhering to guidelines established by relevant regulatory bodies like OSHA helps prevent accidents and maintain worker well-being throughout the project duration.
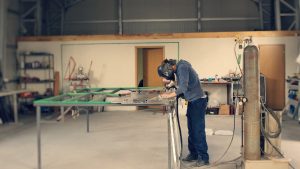
Metal Fabrication Process: Cutting, Shaping, and Joining Metals
When it comes to metal fabrication, three key processes are at the heart of creating sturdy and reliable products: cutting, shaping, and joining metals. Each of these steps plays a crucial role in transforming raw materials into finished goods.
Cutting is where the creation begins, as it determines the shape and size of the metal parts that will be used. Traditional cutting methods such as sawing and shearing are still widely used in today’s industry; however, technological advancements have introduced more precise techniques like laser cutting and plasma arc cutting. These modern methods not only offer greater accuracy but also reduce material waste and increase efficiency.
Once the metal is cut into the desired shape, shaping comes into play. This process can involve bending, rolling, or stamping the metal to achieve specific forms or contours required for the final product. Shaping often requires skilled craftsmanship as well as specialized machinery such as press brakes or rollers. By carefully manipulating the metal through these techniques, fabricators can ensure that it fits seamlessly within larger assemblies while maintaining structural integrity.
Lastly, joining metals is a critical step that brings everything together. Through various welding techniques like MIG (Metal Inert Gas) or TIG (Tungsten Inert Gas), different parts can be securely fused to create a cohesive structure that withstands stressors over time. Welders must possess expertise in choosing appropriate filler materials based on factors such as durability requirements and environmental constraints unique to each project.
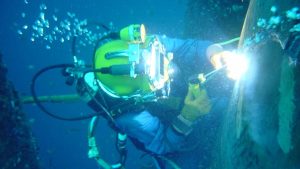
Qualifications and Training Needed for Filipino Ship Welders
Filipino ship welders, renowned for their exceptional skills in the maritime industry, undergo rigorous qualifications and training to ensure they are equipped with the necessary expertise for this specialized field. While a high school diploma is typically the minimum educational requirement, aspiring ship welders often opt to pursue vocational courses or technical education programs focused specifically on welding and metal fabrication. These programs provide hands-on training and theoretical knowledge on various welding techniques, safety practices, blueprint reading, and interpreting technical drawings.
To further enhance their skills, many Filipino ship welders also acquire certifications from reputable organizations such as the Philippine Welding Society (PWS). These certifications validate their competence in specific welding processes and qualify them for work internationally. Obtaining these certifications not only deepens their expertise but also opens up opportunities for higher-paying jobs abroad.
Moreover, continuous professional development is crucial for Filipino ship welders to stay updated with the latest technology advancements in their craft. They constantly seek advanced training courses that cover new welding techniques, equipment usage, and quality control measures. By staying at the forefront of industry standards and embracing emerging technologies like robotic welding systems, Filipino ship welders remain highly sought-after globally for their unmatched skills and dedication to delivering top-notch results.
As you can see, becoming a qualified ship welder requires more than just innate talent – it demands dedication to continuous learning through vocational education programs and obtaining prestigious certifications from industry-recognized organizations.
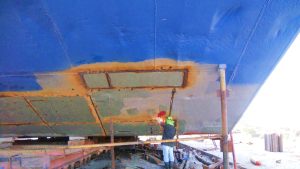
Challenges and Innovations in Ship Welding and Metal Fabrication
Ship welding and metal fabrication in the Philippines are crucial aspects of shipbuilding, ensuring the structural integrity and overall safety of vessels. However, this industry faces unique challenges that continue to drive innovation in order to meet the demands of modern ship construction. One major challenge is the need for welds and metal fabrications to withstand extreme environmental conditions such as corrosion, fatigue, and pressure variations. In response, there have been significant advancements in welding techniques and materials selection to enhance durability and longevity.
Another challenge in ship welding is the need for precise alignment and fit-up of large-scale components during fabrication. The sheer size of ships makes it difficult to align heavy plates or sections accurately without distortion or errors. To address this issue, innovative technologies such as laser scanning and robotic systems have emerged. These tools allow for highly accurate measurements, computer-aided design (CAD), and automated cutting and assembly processes.
In addition to these challenges, environmental concerns have also influenced innovations in ship welding and metal fabrication. New regulations demand reduced emissions from ships, requiring the use of cleaner energy sources like LNG (liquefied natural gas) as fuel. This shift has led to alterations in vessel design, affecting welding procedures in specific areas subjected to extreme temperatures or stress due to different thermal expansion properties.
Overall, ship welding and metal fabrication continue to evolve rapidly with advancements in technology and materials selection driven by various challenges posed by regulatory requirements, demanding environments, size limitations, and accuracy needs during production processes, among others only encouraging more research & development and driving innovation within this space.

Industry Outlook: Future Prospects of Ship Welding and Metal Fabrication in the Philippines
The ship welding and metal fabrication industry in the Philippines is currently experiencing rapid growth, fueled by a combination of factors that include increased demand for ocean transportation and international trade. The country’s strategic location as an archipelago with thousands of islands makes maritime transport a vital mode of transportation. As a result, the need for ships, boats, and other marine vessels has skyrocketed, driving the growth of this industry.
Looking ahead to the future, the prospects for the ship welding and metal fabrication industry in the Philippines remain highly promising. With continued globalization and increasing interest in Southeast Asia as an economic hub, there is expected to be sustained demand for maritime transportation services. Furthermore, growing investments in infrastructure development projects such as ports and harbors will fuel the need for shipbuilding and repair services. The Philippine government has also been actively promoting this sector through various programs and incentives aimed at attracting foreign investments.
While challenges such as competition from neighboring countries exist within this industry, it is evident that ship welding and metal fabrication will play a crucial role in shaping the future of maritime trade in the Philippines. As long as there is continued investment in research and development to enhance technological capabilities, coupled with skilled labor force development programs to meet market demands head-on – this thriving sector can pave its way toward becoming a global leader in shipbuilding and metal fabrication solutions.
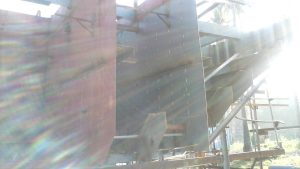
How to Choose the Best Ship Welding and Metal Fabrication Shipyard in the Philippines?
When it comes to ship welding and metal fabrication in the Philippines, choosing the best company for your needs is crucial. With numerous options available in the market, it can be overwhelming to make the right decision. To ensure you select an experienced and reliable company, there are several factors to consider.
First, examine their track record and experience in ship welding and metal fabrication projects. Look for companies that have a proven history of delivering high-quality work on time. Check if they have worked on similar projects in the past and inquire about their success rate.
Second, assess the qualifications and skills of their welders and fabricators. Look for certifications such as AWS (American Welding Society) or CSWIP (Certification Scheme for Welding Inspection Personnel). It is important to know that they possess the necessary expertise to handle complex tasks effectively.
Last, take into account their facilities and equipment. A reputable company should have well-maintained machinery and tools required for ship welding and metal fabrication. Additionally, check if they adhere to international standards such as ISO 9001:2015 certification, which ensures quality management systems are in place.
By scrutinizing these aspects thoroughly, you can confidently choose a ship welding and metal fabrication company in the Philippines that will meet your specific requirements with professionalism and excellence.
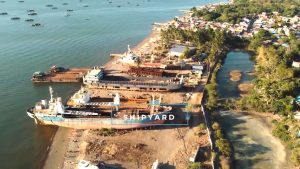
Are you Looking for the Best Ship Welding and Metal Fabrication Dockyard in the Philippines?
Amaya Dockyard & Marine Services Inc. (ADMSI) is a renowned ship welding and metal fabrication company in the Philippines that offers top-notch services to its clients. With a strong commitment to quality and customer satisfaction, ADMSI prides itself on being one of the best in the industry.
- Email us: info@amayadockyard.com
- Call our 24-hour hotline: +63 917 633 0479
- Viber: +63 917 633 0479
- WhatsApp: +63 917 633 0479
- Facebook Messenger: Click here
- Click here to inquire
What sets ADMSI apart is our team of highly skilled and experienced Filipino welders and fabricators who ensure that each project is handled with professionalism and precision. Whether it’s welding repairs, metal fabrication, or even custom vessel designs, ADMSI has the expertise to deliver exceptional results.
In addition to our technical skills, ADMSI also places a strong emphasis on safety standards and environmental responsibility. We adhere strictly to international regulations and use cutting-edge technology to minimize our carbon footprint while providing efficient services.
When it comes to ship welding and metal fabrication, you can trust Amaya Dockyard & Marine Services Inc. for the highest quality workmanship combined with unmatched expertise.
Final Thoughts: Ship Welding and Metal Fabrication in the Philippines
In conclusion, ship welding and metal fabrication in the Philippines is a thriving industry that plays a crucial role in the country’s maritime sector. The skilled workforce, coupled with modern facilities and technologies, have allowed Philippine shipyards to become regional leaders in shipbuilding and repairs. This has not only enhanced the country’s economy but also created job opportunities for thousands of Filipinos.
Moreover, what sets the Philippines apart from other countries in terms of ship welding and metal fabrication is its adaptability and ability to meet international standards. The country has made significant investments in training its workforce to ensure they have up-to-date knowledge and skills required for complex projects. This has led to an influx of international clients who rely on Philippine shipyards for their expertise.
The future looks bright for the ship welding and metal fabrication industry in the Philippines. With increasing demand for new vessels as well as repair services, there is ample opportunity for growth and expansion. As technology continues to advance, it is essential for local businesses to embrace automation and digitalization to stay ahead of the competition globally. The strategic location of the Philippines also offers logistical advantages, making it an attractive choice for both regional and global clients.
Overall, ship welding and metal fabrication form a vital part of the maritime industry in the Philippines. Through continuous innovation, commitment to excellence, and dedication to meeting international standards, this sector will continue to thrive and contribute significantly to the country’s economy while positioning itself as a competitive player on the global stage.